
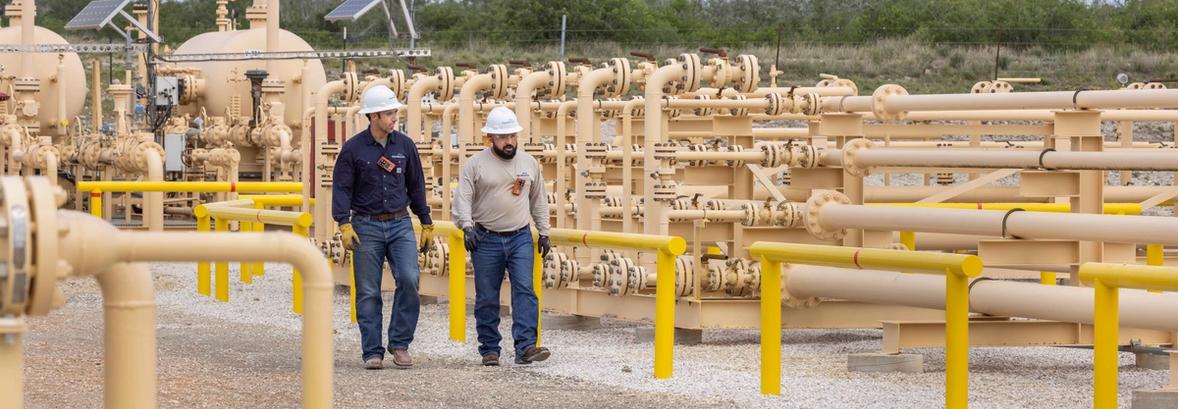
Spill Prevention
In all resource plays, Marathon Oil stores both hydrocarbons and untreated produced water at our production facilities in storage tanks with secondary containment to mitigate the risk of spills to the environment. Produced water may also be stored in open-top tanks during fracturing and flowback operations when crews are onsite and able to respond quickly to a spill. To help protect wildlife, we use active deterrents such as netting, strobe lights, flags and air horns for temporary pits that may hold recycled water during completion activities.
Our spill prevention activities are governed by the regulatory compliance elements of our Responsible Operations Management System (ROMS), while emergency preparedness and response activities are covered under the ROMS Emergency Preparedness and Community Awareness element.
If a spill does occur, we activate our comprehensive response capabilities to contain the spill and help protect the surrounding environment. We train local, regional and corporate response teams and conduct drills and exercises to maintain their readiness. We also have a response network of contractors and consultants. When investigating spills and discharges to determine their cause, we look at both the actual and potential severity of the spill. We take incident-specific actions and, if necessary, broad corrective actions including remediation. We completed produced water-control mitigation efforts in the Eagle Ford and the Bakken where we operate our own water disposal infrastructure.
- ᵃ Data includes spills released off-site ≥ to 1 barrel. All spills to the environment are remediated per state requirements.
- ᵇ ~47,500 barrels of 2019 total spill volume was produced water.
How are we doing?
Your opinion matters. Please take a moment to let us know how useful you find the content on this page.
If you’d like to give us your feedback on the entire report, please fill out the complete survey for the 2022 report.